As the key driver of the Group’s overall business philosophy, Tiong Seng is focused on achieving construction productivity and efficiency through developing a strong base of engineering talent and leveraging technology as a force multiplier.
​
Tiong Seng Engineering Solution (TSES), a leading engineering specialist, offers a stop solution in the latest innovative green technologies and sustainable Design for Manufacturing and Assembly (DfMA) solutions in the built environment sector, propelling towards future construction. These methods are environmentally friendly, produce less noise pollution, more efficient and less labour-intensive. These capabilities enhances our ability to design and build for Green Mark certified buildings which places emphasis on the usage of sustainable construction technologies.

GREEN CONSTRUCTION METHODOLOGY
DESIGN FOR MANUFACTURING & ASSEMBLY
Prefabricated Prefinished Volumetric Construction (PPVC)
Prefabricated Bathroom Units (PBU)
​
Modular MEP
​
CONSTRUCTION TECHNOLOGY
Building Connection
Voided Slab

Prefabricated Prefinished Volumetric Construction (PPVC)
Tiong Seng was an early adopter of advanced formwork and precast technologies since the 1990s and we have innovatively developed in-house and patented our Lithe™ Prefabricated Prefinished Volumetric Construction (PPVC) construction method that embraces safety, quality, and productivity.
This manifested in the setting up of Tiong Seng Prefab Hub in 2012 - Singapore's first Integrated Construction and Precast Hub (ICPH). This provided a competitive edge for Tiong Seng's subsequent projects, having built its own capabilities. Additionally, this advanced multi-storey building equipped with an automated precast concrete production line is in line with BCA's drive towards DfMA, a key pillar in the Construction Industry Transformation Map (ITM) and sets a precedence for the local construction industry to emulate.
Prefabricated Bathroom Units (PBU)
Since 2006, Tiong Seng started adopted adopting PBU technology and is one of Singapore's largest PBU manufacturers. Our in-house Lithe™ PBU utilises Ultra High Performance Concrete (UHPC) for additional durability and is 60% lighter in weight compared to conventional concrete PBU. These units preassembled off-site in factory controlled environment ensures high quality finishing.
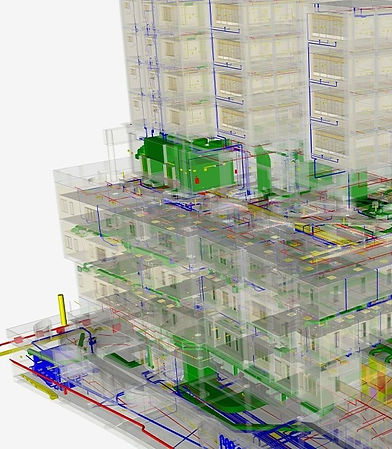
Modular MEP
Driven by our commitment to build up our internal competencies in DfMA, Tiong Seng is working towards the establishment of Prefab MEP. This capability serve to lean the manpower required and time savings of up to 60%. This further strengthens Tiong Seng's position as a one stop solution provider in sustainable construction solutions in the built environment industry.
Building Connection
The collaboration between Tiong Seng's wholly-owned subsidiary, Robin Village International (RVI), and Splice Sleeve Singapore and Splice Sleeve Japan, resulted in TS Sleeve - a super-high strength grout-filled type deformed reinforcing bar splices for precast concrete members. Its ability in earthquake resistance and ease of construction enables it to be widely applicable across various buildings types.
Voided Slab
COBIAX, a wholly-owned subsidiary of Tiong Seng, holds an internationally patented technology in voided slab. The reinforced concrete slab incorporates air-filled voids in certain areas of the slab to reduce the volume of the required concrete by up to 30%, allowing for greater degrees of design flexibility. This also translates into a dramatic reduction in carbon dioxide emission of as much as 210 kg for every cubic metre of concrete displaced, supporting greater sustainability in construction.
​
TSES has gathered an impressive track record of voided slab implementation in Hotel, Residential, Commercial, and Industrial buildings in Singapore.

Kallang Polyclinic & Long Term Care Facility
Awarded the BCA Green Mark Platinum Award in 2019, the 10-storey integrated healthcare infrastructure is the first hospital project in Singapore to utilise hybrid PPVC methodology. By adopting over 130 Hybrid (Steel Frame) PPVC Modules, the building’s deadload was substantially reduced, allowing for lesser heavy equipment on-site.
Given the complexity of the project, BIM and Integrated Digital Delivery (IDD) was implemented on the onset for multi-disciplinary coordination. This led to the reduction of construction timeline by 25% equivalent to over 5,000 Hours.
​
Watch the video to find out more!
​
featured project